Nutrilo: Kardex Mlog provides logistics boost
12 September 2024, Company News
At the Nutrilo GmbH production and logistics location in Cuxhaven, Kardex Mlog has extended the facility with a single-aisle, automated small-parts storage warehouse containing 3,124 container spaces for storing raw materials and finished goods. Automated conveying technology connects the new plant to the goods receipt, production, picking, and shipping areas. In its role as general contractor, Kardex Mlog was also responsible for coordination with the additional trades involved in the project. Kardex Mlog is already working on plans for a possible further expansion step at the same location: A four-aisle, automated high-bay warehouse with more than 5,000 pallet storage spaces.
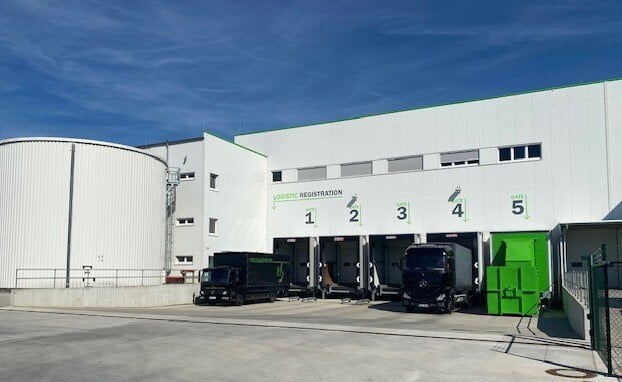
Products from Nutrilo GmbH are popular with customers who boost their diet with vitamins, minerals, and trace elements. The company is a globally active contract manufacturer of diverse food supplements, which it supplies to drugstores, pharmaceutical companies, and food retailers. To meet the growing demand in the future, the company increased its logistics capability at its headquarters in Cuxhaven to include an automated storage area.
In-house manufacturing in Germany
Kardex Mlog submitted the successful tender for the Nutrilo project. “We were very impressed by Kardex Mlog’s many years of experience, excellent references, and wide-ranging portfolio – with Kardex, we could obtain the entire solution from a single source,” explains head of logistics, Peter Daniel. In fact, a major part of the plant was produced by Kardex Mlog at their German manufacturing location. Of the total project scope, just three floor-put-down devices, two high-speed doors, and five conveyor system closures were provided by other suppliers.
The plant control system also deploys solutions from Kardex Mlog: Order management and storage space management are carried out by the Kardex MFlow material flow system, whereas plant visualization is managed using Kardex MVisu software. Kardex MFlow has interfaces to the underlying controls of the conveying systems, vertical conveyors, scales, and the stacker crane. The software communicates with Nutrilo’s SAP EWM warehouse management system. SAP is the central host system.
The design includes a single-aisle, fully automated, small parts warehouse with the appropriate conveying technology for storage and retrieval and connection to production through pallet and container conveying technology. The entire plant runs five days a week with three-shift operations. In both storage areas, the ambient temperature is between +15°C and +30°C.
Container conveying system with automatic control
The small parts storage facility, around 37.5 meters long and containing 3,124 storage spaces, enables storage and retrieval of up to 120 containers per hour. The plastic containers, which measure 600 x 400 x 420 mm and 600 x 400 x 200 mm, weigh up to 25 kilograms. These are transported by a stacker crane of type Kardex MDynamic 25/11 with a construction height of 10,220 mm. The small parts storage is supplemented by a container conveying system with automatic control and plant visualization. The conveying technology connects the small parts storage with goods receipt, production, a narrow-aisle warehouse, and the picking area.
When a container is placed on the conveying technology in the goods receipt or production area, it is immediately weighed automatically. It is then scanned automatically before undergoing a contour check. Based on the data collected, the control system determines whether the container is to be stored. If so, a transport order is sent to the Kardex MFlow material flow computer and the order is executed by the stacker crane. The small part containers required for pick orders are called up from the small parts storage and are transported to the U-shaped picking area. Once the parts are withdrawn, the containers return to the small parts storage area.
On-time handover
Construction of the entire plant with small parts storage, conveying technology, and control system was completed within 12 months and handed over to Nutrilo on schedule. “During the entire project phase, we received optimal support from Kardex Mlog and were kept fully informed of the progress at all times. The on-schedule handover was the icing on the cake,” says deputy logistics manager, Ralf Schröder.
Nutrilo concluded a comprehensive service contract with Kardex Mlog to secure top performance and avoid malfunctions and breakdowns. This includes remote access to the plant and emergency support on site. The parties also agreed on a six-monthly maintenance of the small parts storage and conveying technology, alongside an annual occupational safety inspection of the plant. Kardex Mlog has also set up a hotline for the PLC control, the electrical system, and the material flow system. This is available to Nutrilo around the clock on all five workdays.
Thinking ahead
About Kardex Mlog
The company has more than 55 years of experience in the planning, implementation, and maintenance of fully automated logistics solutions. The three business sectors - Greenfield installations, Refurbishment, and After−sales service – draw upon its in-house manufacturing facility in Neuenstadt. Kardex Mlog is part of the Kardex Group and employs 353 people. In 2023 the company achieved revenues of €113 million.