Im österreichischen Hohenems hat Kardex Mlog als Generalunternehmer für die auf Bewegungs-Systeme für Möbel spezialisierte GRASS Gruppe ein hochautomatisiertes Hochregallager mit rund 38.800 Palettenstellplätzen gebaut. Zu den Besonderheiten gehören eine vollautomatische Lkw-Entladung, eine effiziente Ware-zur-Person-Kommissionierung mit einem Kommissionierpuffer und zwei Warenausgangspuffer. Startpunkt des ehrgeizigen Bauprojekts war ein Ideenwettbewerb.
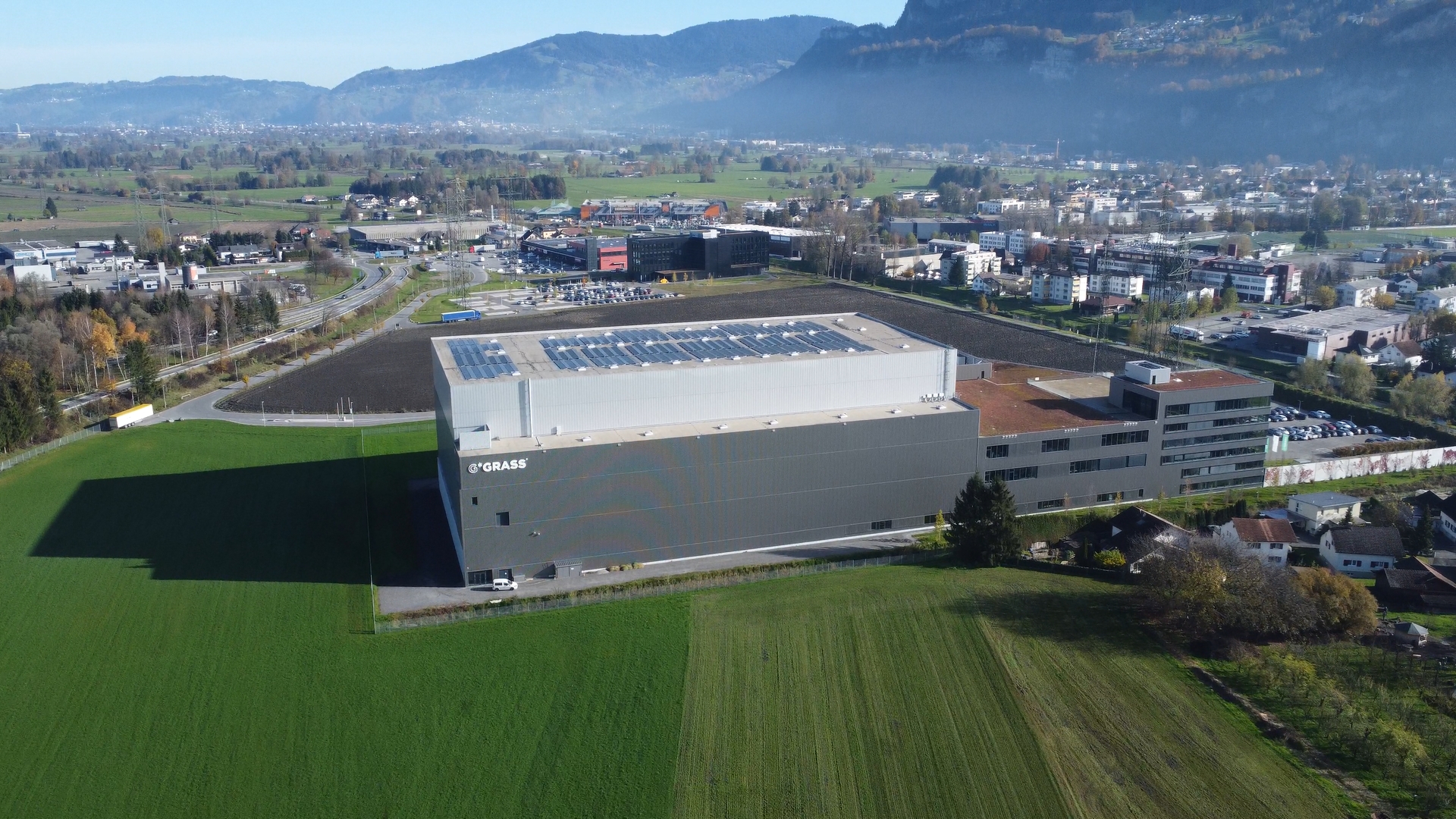
Sanft gleitende Schubladen und elegant schließende Schranktüren: Mit raffinierten Scharnieren, Auszügen oder Klappen-Systemen tragen moderne Möbel zu einem hohen Wohnkomfort bei. Auf diesem Gebiet zählt die österreichische GRASS-Gruppe zu den führenden Spezialisten mit über 200 Vertriebspartnern in 60 Ländern. Um die Bestellvorgänge zu vereinfachen und um die Lieferzeiten für die weltweiten Kunden zu verkürzen, wurde die Fertigwaren-Logistik aller europäischen Produktionswerke im Jahr 2020 an einem neuen Standort im österreichischen Vorarlberg zentralisiert. Zuvor wurden die Bestellungen an vier Außenlagern abgefertigt, was zu einer hohen Komplexität der Prozesse führte.
Gute Erfahrungen aus anderen Projekten
Die zur Würth-Gruppe zugehörige GRASS GmbH sicherte sich deshalb bereits 2016 ein 52.000 qm großes Grundstück bei Hohenems, um darauf ein idealtypisches Logistikzentrum zu errichten. „Auf der Suche nach dem besten Konzept hatten wir einen Ideenwettbewerb ausgeschrieben, an dem sich acht Intralogistikanbieter beteiligten“, erinnert sich Projektleiter Jürgen Moritsch. „Für Kardex Mlog sprachen am Ende nicht nur die guten Erfahrungen aus anderen Projekten innerhalb der Würth-Gruppe. Uns überzeugten auch die sehr engagierten Mitarbeiter und vor allem die durchgängige Planung mit zahlreichen guten Ideen für hocheffiziente Abläufe“, so Moritsch. Außerdem suchte man einen Lieferanten, „mit dem wir auch im Hinblick auf Folgeprojekte eine langfristige Partnerschaft auf Augenhöhe aufbauen konnten.“
Das Distributionszentrum mit rund 38.800 Palettenstellplätzen wurde am 1. Juni 2020 in Betrieb genommen. Es ist das größte Logistik-Bauprojekt, das bis dato im österreichischen Bundesland Vorarlberg realisiert wurde. GRASS investierte hier 70 Millionen Euro.
Entladen in nur 90 Sekunden
Bereits das Entladen der LKW im Wareneingang und das anschließende Einlagern der durchschnittlich 800 Paletten pro Tag läuft hier vollautomatisch – wobei das System fünf unterschiedliche Palettentypen verarbeiten kann. Angeliefert werden die Paletten im Rahmen des Werkverkehrs direkt aus den umliegenden Produktionsstätten der GRASS-Gruppe. Die eigenen Sattelzüge verfügen über spezielle Auflieger, deren Ladeflächen über eine im Boden versenkte Fördertechnik verfügen. Mit dem Andocken wird die mobile mit der stationären Fördertechnik verbunden und das Entladen beginnt – wie von Geisterhand rollen die Paletten aus den Fahrzeugen. „Nach rund drei Minuten ist der Auflieger leer und der LKW kann seine Fahrt fortsetzen“, betont Logistikleiter René Malojer. Ein weiterer Vorteil der schnellen Entladung ist, dass die vereinnahmten Paletten wesentlich schneller für die Kunden verfügbar sind.
Jede Palette ist mit einem QR-Code versehen, der auf dem Weg in das elfgassige Hochregallager automatisch ausgelesen und mit den Daten im Warenwirtschaftssystem abgeglichen wird. „Unter anderem gibt der Barcode darüber Auskunft, um welchen Palettentyp es sich handelt. Dementsprechend entscheidet die Software, in welchem Teil des Hochregals ein Lagerplatz gesucht wird“, erklärt Manuel Bonner, der als Mitglied der IT-Abteilung bei GRASS das Lagerverwaltungssystem betreut. Bei Unstimmigkeiten werden die jeweiligen Paletten automatisch auf eine NIO-Strecke (NIO = „Nicht in Ordnung“) ausgeleitet und dort manuell untersucht beziehungsweise korrigiert. Alle übrigen Paletten werden direkt über eine Förderstrecke zum Aufnahmepunkt des Hochregals transportiert, wo sie von einem der 11 Regalbediengeräte (RBG) vom Typ Kardex MSingle B 1000/34-ET empfangen und auf eine der 22 Regalebenen gehoben werden. Die von Kardex Mlog am Standort Neuenstadt am Kocher aus einem Stück gefertigten RBGs sind 34 m hoch und schaffen bis zu 40 Doppelspiele pro Stunde.
Ergonomisch optimierte Pickplätze
75 Prozent der hier eingelagerten Paletten verlassen das Lager wieder als Vollpaletten. Die übrigen 25 Prozent dienen als Quellpaletten für die Ware-zur-Person-Kommissionierung, die an zwei ergonomisch optimierten Pickplätzen stattfindet. Diese befinden sich auf einer Bühne, die vom Erdgeschoss über acht Scherenhubtische mit den Quellpaletten versorgt werden. Die Kommissionierer können sich die Quellpaletten Lage für Lage in der optimalen Höhe andienen lassen und die Packstücke mit Vakuumhebern auf die Zielpalette schichten. Zum Absichern der Bediener beim automatischen Wechsel der Ziel- und Quellpaletten ist jeder Arbeitsplatz mit Trittschaltmatten ausgestattet. Solange sich ein Picker im Gefahrenbereich befindet, sind die Scherenhubtische abgeschaltet. Leerpaletten werden automatisch über Leerpalettenstapler und Verfahrwagen bereitgestellt. Das Gewicht der Paletten wird über eine integrierte Waage erfasst. Sämtliche Leerpaletten sind mit einer Paletten-ID eindeutig gekennzeichnet.
Zudem verfügt jeder Kommissionierplatz über einen Leitbildschirm und fest zugewiesene mobile MDEs. Die Geräte sind pro Platz sowie über den gesamten Arbeitsbereich miteinander gekoppelt und kommunizieren als Einheit mit der Fördertechnik. Die Bildschirme leiten den Nutzer visuell und liefern ihm zugleich eine multimediale Übersicht. In Echtzeit erhält er weiterführende Informationen zum aktuellen Pick und seinem Arbeitsvorrat. Durch dieses leicht verständliche System konnte die Anlernzeit neuer Picker um 80 Prozent verringert werden. Und nicht nur das: „Die zuvor schon niedrige Fehlerquote konnten wir durch diese Anordnung nochmals um 70 Prozent verringern und bewegt sich jetzt im Promillebereich“, betont Jürgen Moritsch. Eine automatische Gewichtskontrolle der Zielpaletten trägt ebenfalls zu der extrem hohen Qualität der Kommissionierung bei.
Drei Pufferlager für Nachschub und Warenausgang
Der An- und Abtransport der Quellpaletten erfolgt über Rollenbahnen, die Teil der umfangreichen Fördertechnik sind. Dabei kommen die Paletten entweder direkt aus dem Hochregal oder aus einem Nachschubpuffer vom Typ Kardex MSequence mit einer Kapazität von 82 Paletten. Das 12 m hohe Nachschub-Regal befindet sich direkt hinter einem der beiden Pickplätze und wird vollautomatisch von einem RBG vom Typ Kardex MSingle A bedient. Die Durchsatzleistung liegt bei 43 Doppelspielen pro Stunde.
Zwei weitere Pufferspeicher vom Typ Kardex MSequence mit einer Kapazität von insgesamt 420 Paletten wurden im Warenausgang installiert. Hier arbeiten zwei RBGs vom Typ Kardex MTwin S, die bei doppelttiefer Ein- und Auslagerung für einen Durchsatz von rund 54 Doppelspielen pro Stunde sorgen und die geplanten Touren vorsequenzieren. Das Auslagern der bis zu 1.500 Paletten pro Tag erfolgt innerhalb eines Auftrages nach der Maßgabe „schwer vor leicht“, um das spätere Verladen zu optimieren. „Mit Hilfe der beiden Warenausgangspuffer können wir jeden LKW innerhalb von nur 45 Minuten voll beladen und abfertigen“, berichtet René Malojer. Bei ihrer Ankunft im Logistikzentrum erhalten die vorangemeldeten Fahrer einen Pager, der sie über den Start der Beladung und das zugeordnete Verladetor informiert. In der Regel wird die komplette Ladung der bis zu 80 Paletten pro LKW bereits zwei Stunden zuvor vom Hochregal in den Warenausgangspuffer umgelagert. „Dadurch können wir auch dann schnell handeln, wenn der Fahrer früher als geplant bei uns erscheint“, erklärt Manuel Bonner.
Rationell, sicher und transparent
Fazit: Mit vielen Ideen und gründlicher Planung hat Kardex Mlog gemeinsam mit der GRASS GmbH ein hocheffizientes und mitarbeiterfreundliches Logistikzentrum realisiert. Durch den weitgehend automatisierten Materialfluss, die ergonomische Kommissionierung und die drei integrierten Pufferspeicher konnte der Personalbedarf auf 17 Mitarbeitende begrenzt werden. Zugleich wurden Qualität und Liefergeschwindigkeit erhöht, während sämtliche Abläufe völlig transparent nachverfolgt werden können.
Hintergrund: GRASS GmbH Bewegungs-Systeme
Die GRASS-Gruppe ist eine global operierende Unternehmens-Gruppe, die sich als Entwicklungspartner und Systemanbieter der Möbelindustrie auf Bewegungssysteme spezialisiert hat. Zum Portfolio gehören Führungs- und Auszugs-Systeme sowie Scharnier- und Klappen-Systeme. Das im Jahr 1947 gegründete Unternehmen mit Sitz in Höchst (Vorarlberg, Österreich) beschäftigt an 19 Standorten knapp 1.800 Mitarbeiter und verfügt über mehr als 200 Vertriebspartner in 60 Ländern. 2021 erwirtschaftete GRASS einen Umsatz von 467 Millionen Euro. Seit 2004 ist GRASS Teil der Würth-Gruppe.
Über Kardex Mlog
Kardex Mlog (www.kardex.com) mit Sitz in Neuenstadt am Kocher ist einer der führenden Anbieter für integrierte Materialflusssysteme und Hochregallager. Das Unternehmen verfügt über mehr als 55 Jahre Erfahrung in der Planung, Realisierung und Instandhaltung von vollautomatischen Logistiklösungen. Die drei Geschäftsbereiche Neuanlagen, Modernisierung und Customer Service stützen sich auf die eigene Fertigung in Neuenstadt. Kardex Mlog gehört zur Kardex-Gruppe und beschäftigt 305 Mitarbeitende, der Umsatz für das Jahr 2021 lag bei 89 Mio. Euro.
Weitere Informationen:
MLOG Logistics GmbH
Wilhelm-Maybach-Straße 2
74196 Neuenstadt am Kocher
Pressereferentin:
Bettina Wittenberg
Tel.: +49 7139 / 4893-536